Advanced Grasp Generation Techniques for Robotic Manipulation
Project Overview
This project innovates in the field of robotic manipulation by developing sophisticated algorithms for grasp generation using simulations that integrate real-world physics and complex scenarios. The focus is on enhancing the accuracy and reliability of robotic grips in cluttered environments, which is crucial for tasks ranging from automated assembly in manufacturing to precise operations in surgical robotics.
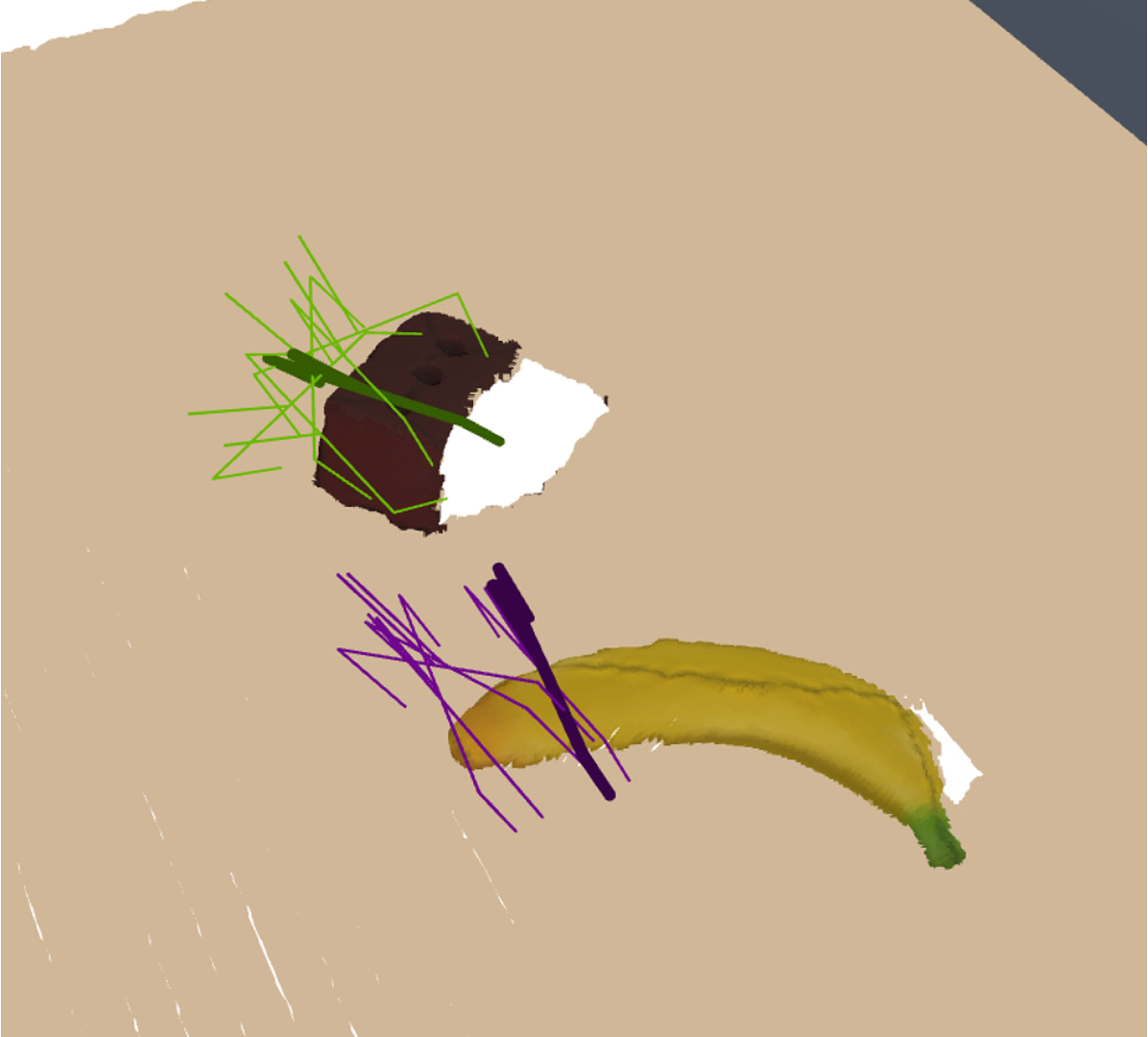
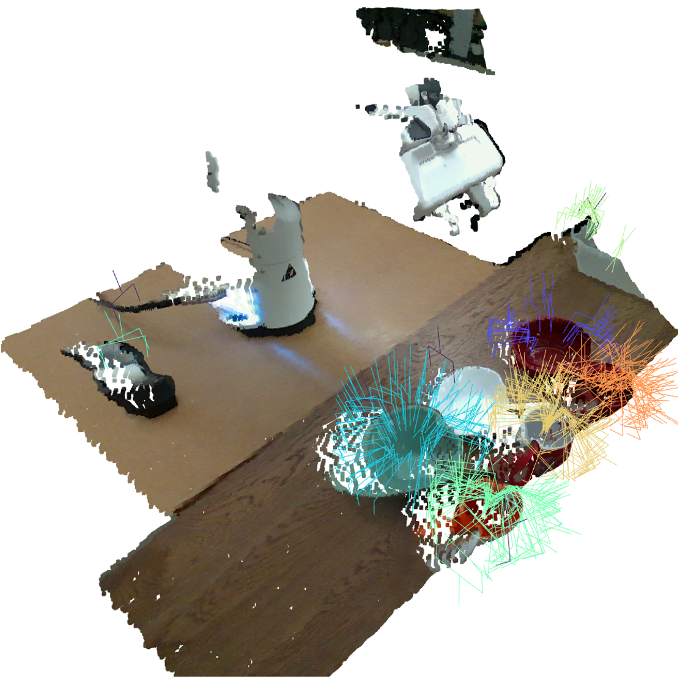
Technical Highlights
- Simulation Setup: Utilizes a detailed simulation environment with a Franka Gripper robot and YCB clutter objects to mimic real-world conditions closely. This setup allows for precise testing and refinement of grasp techniques.
- Grasp Pose Generation: Employs advanced algorithms to dynamically generate grasp poses based on object geometry and environmental context, significantly enhancing the adaptability of the robotic system.
- Multi-view Point Cloud Integration: Incorporates data from multiple cameras to create a comprehensive 3D representation of the environment, which improves the robot's understanding of its surroundings and the positioning of objects.
- Antipodal Sampling: Utilizes geometric and force closure properties to determine optimal grasp points, ensuring stability and minimizing the risk of slippage.
- Real-time Adjustments: Features the capability to adjust grip strategies in real-time based on feedback from environmental interactions, increasing the success rate of grasps under varying conditions.
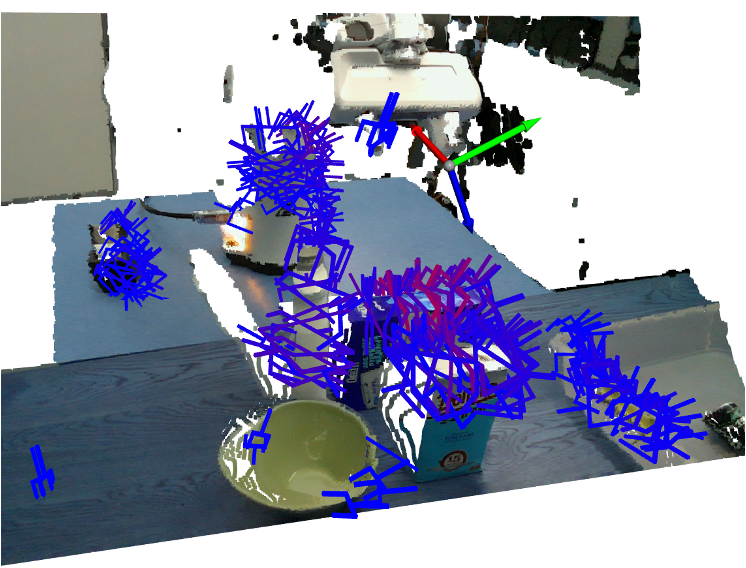
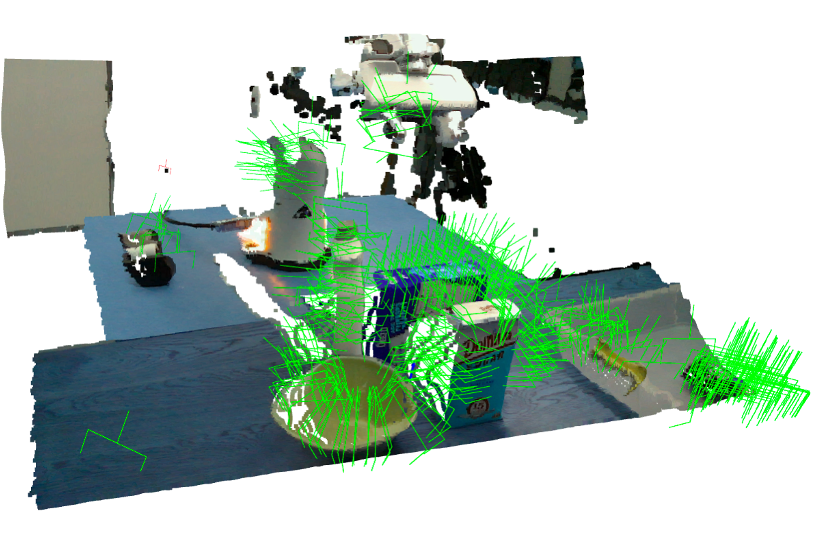
Innovations and Contributions
- Robust Grasp Synthesis: Through the use of simulated environments, the project develops robust algorithms that can predict and execute effective grasps even in densely packed spaces.
- Enhanced Object Recognition and Handling: Integrates advanced vision systems and sensor feedback to accurately identify and manipulate a wide range of object shapes and sizes.
- Adaptive Learning Models: Incorporates machine learning techniques to continually refine grasp strategies based on past performance, which enables the robotic system to learn from its environment and improve over time.
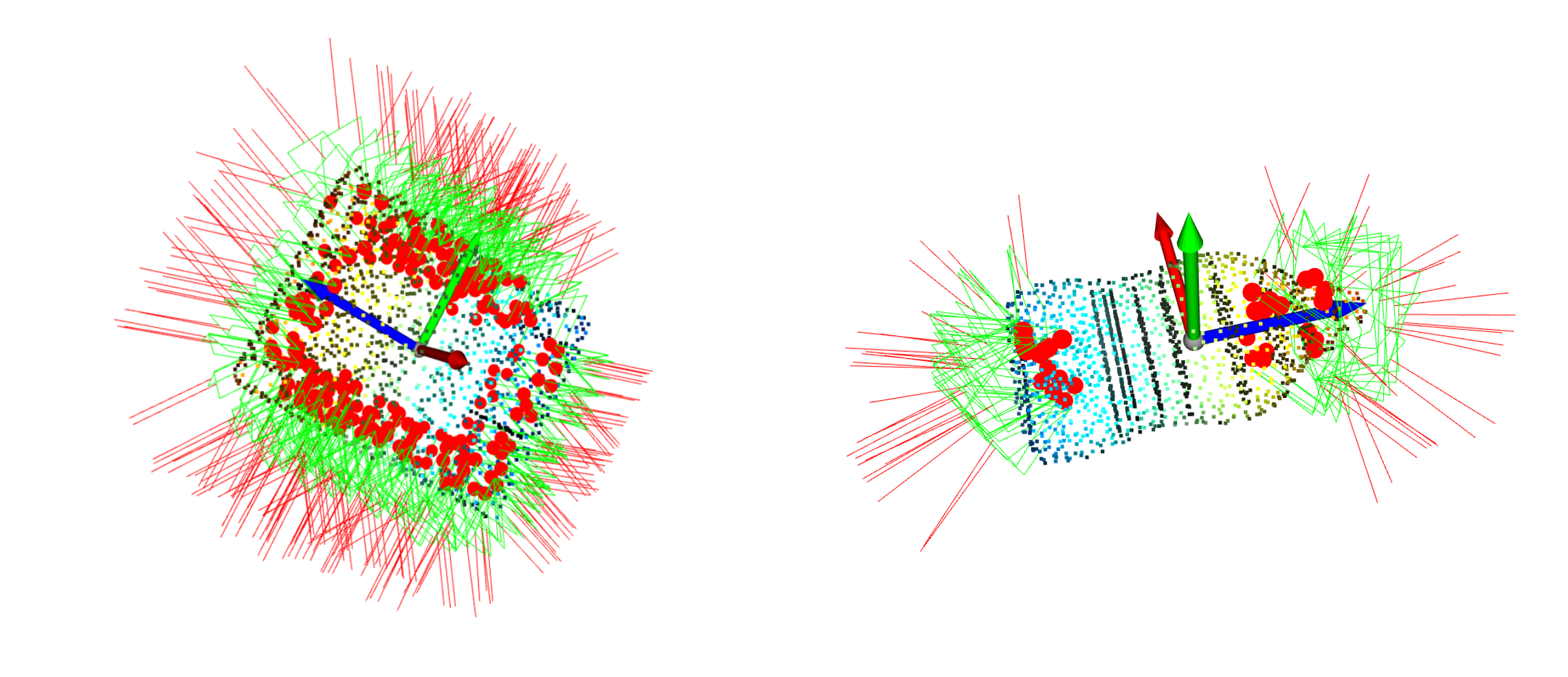
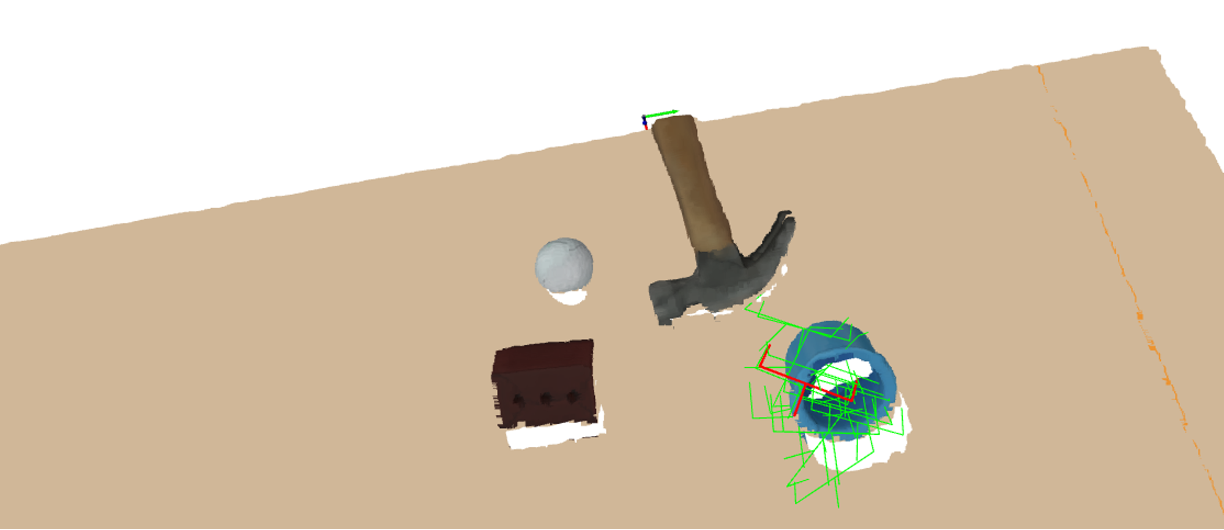
Real-world Applications
The technologies developed in this project have significant implications for several industries:
- Manufacturing: Robots equipped with these advanced grasping techniques can perform more complex assembly tasks with higher precision and lower error rates.
- Healthcare: In surgical settings, the enhanced manipulation capabilities can lead to more delicate and safe interactions with soft tissues and small, intricate medical devices.
- Logistics: Automates the packaging and handling processes, allowing for more efficient sorting, packing, and transporting of goods.
Conclusion
This project not only pushes the boundaries of robotic manipulation through innovative grasp generation techniques but also sets a new standard for the integration of robotics in practical applications. The blend of simulation-based testing and real-world application demonstrates a scalable path for robotics research that significantly enhances the capabilities of autonomous systems in complex environments.
Further Research Directions
Future work will focus on expanding the adaptability of grasp techniques to more diverse materials and environmental conditions, as well as integrating greater degrees of sensory feedback to further enhance the precision and reliability of robotic manipulations.